Watch case manufacturing is the most important step in watchmaking. A well designed and crafted watch case looks nice and brings a brand everlasting value. Some watch lovers are curious to know how watch cases are made. And some startup owners will launch their own watch brand so want to get some understanding of watchmaking. This post will give you a general idea of the watch case manufacturing process.
Designing & Engineering
The very first step is watch case designing. An experienced watch designer can transform ideas into sketches. A watch engineer will then evaluate the sketches and if everything works, produce technical drawings (shown below). This set of drawings include that for the case body, bezel, glass cover, crown, back cover, etc. Sometimes 3D renderings are created.
Die Casting, CNC Machining, & Polishing
To manufacture a custom watch case, custom die cast molds have to be made first. The use of die casting guarantees that all cases made are identical. Die cast machines produce what is called “raw cases”, which have rough edges but the outline of finished ones.
The raw cases are then sent to be machined. CNC machining makes watchmaking efficient. The technical drawings are input into the computers and machine operators simply press a few buttons, and everything is done on autopilot.
When the machining is finished, the cases are sent to be polished. This is a relatively time consuming process, because this is all done manually. The case finish can be polished, brushed, and sandblasted or sometimes a mix of polishing and brushing.
Engraving & Plating
Custom watch cases usually have their own branding. The logos can appear on the crown, back cover and even body of the case. Modern engraving technology is so advanced that almost any texts or images can be engraved on the watches.
A watch collection usually has a few color variations, so the last step in custom watch case manufacturing is called plating. This is a step to “color” the watch case. It is not dyeing but an electrical chemical process instead. The most common plating colors are rose gold, yellow gold, black, gunmetal, brown, and blue.
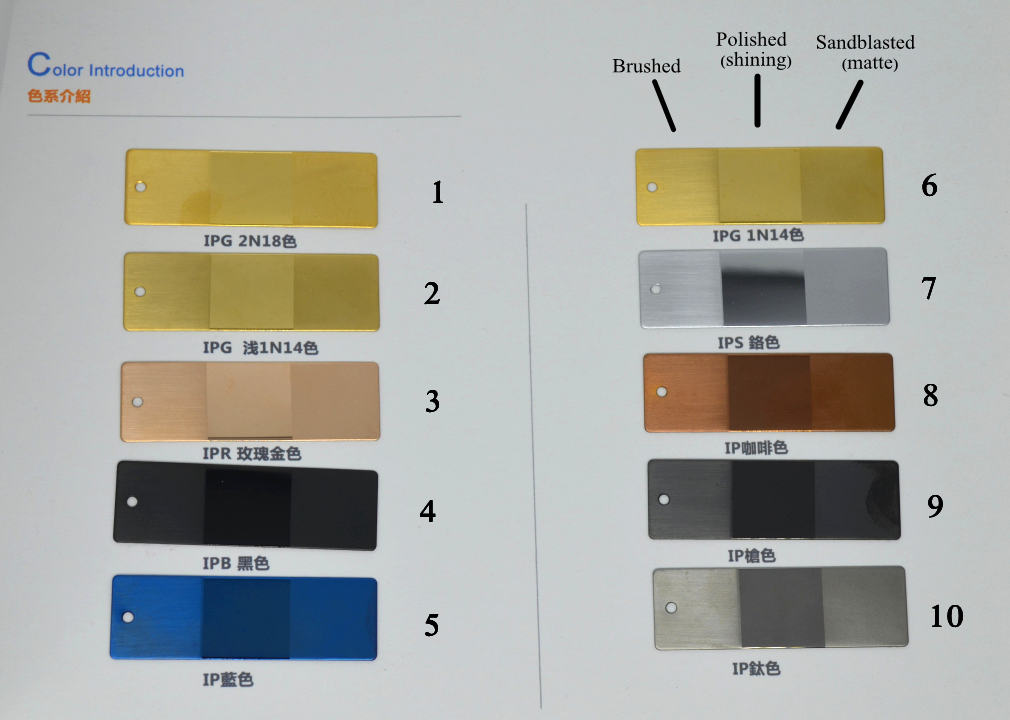
Hope this post helps you understand the custom watch case manufacturing process. If you have any case to be custom made, please contact Ascend team. Thank you!